I. Introduction: In today’s society, with the continuous advancement of science and technology, more and more modern medical devices have developed rapidly, especially electronic instruments that are in direct contact with the human body, in addition to the increasingly high requirements for the performance of the instrument itself. There are more and more concerns about human safety, such as: cardiac puncture monitors, ultrasound, maternal and child monitors, baby incubators, life monitors, etc., which are in close contact with the human body, that is, patients use The instrument should not cause any electric shock or other danger to the human body due to the use of the instrument. Second: the choice of medical power: Medical electronics, unlike other electronic and power electronics that target mass-market and cost-conscious consumer electronics and other low-cost products, medical electronics have many more rules to follow. If the designer is responsible for system power design, the first question to consider for the system power supply section is: purchase or manufacturing related solutions? Since medical electronics production is generally relatively low, designers must consider buying or making problems. Medical electronics designers rarely consider designing their own off-line power supplies. Because the investment required for this particular design and test does not match the final production scale; equipment manufacturers will find it difficult or impossible to share the investment in the design phase. Therefore, it is more cost-effective to purchase power directly from companies that already have the corresponding professional design capabilities and testing techniques. 1. Price: In commercial application design, if the quality is guaranteed, it is easy for people to directly select the lowest-priced power product after shopping for three. At this time, the lowest-priced but “decent” products are often winners, while the best products are unpopular. This is not bad for disposable electronic products that are quickly abandoned or need not be repaired, but what if the designer chooses such a power supply to use the medical system? The value of medical electronics is high and some key tasks need to be accomplished. If the medical system fails, the consequences are not just to miss a game or to take the wrong car. The normal operation of medical equipment, especially the power supply of medical equipment, must comply with safety, leakage, EMI-RFI radiation and protection regulations. These standards and related safety regulations constitute a set of strict normative requirements. Power supplies used in such demanding applications must meet stringent specifications for insulation measures to prevent patient and medical personnel from getting an electric shock. EMC is also a key issue, including how to reduce electromagnetic radiation and how to protect electromagnetic radiation. Therefore, for the design of medical power supply, the first choice must be the quality and reliability of the product. Often, designers are confused about commercial power supplies and medical power supplies, and manufacturers that manufacture low-cost power supplies for the mass market may sell these commercial power supplies as medical power supplies without modification. In this regard, buyers must be careful, because the choice of such power products will lead to terrible consequences. Therefore, designers need to understand the relevant regulations and regulations. So, what are the problems involved in choosing a medical power supply? The power supply for medical equipment must comply with safety, leakage, EMI-RFI radiation and protection regulations. Other issues, such as whether it is produced by a GMP-certified factory? 2. GMP qualification: The US Food and Drug Administration (FDA) requires medical products to be manufactured in factories that are GMP-qualified (ie, have good practices). This is a set of quality certification system that should be required by the manufacturer in addition to the traditional ISO9000 certification to prove that its quality control procedures comply with GMP regulations. Similarly, China also has strict control over medical power sources, such as CE and UL medical certification. The GMP specification stipulates that manufacturers must have component quality control procedures and have relevant documentation. When selecting a medical power supply, can you ask the manufacturer to have a component quality control procedure? Are there quality data and test files? Ask what is the procedure and ask for the relevant documents. Manufacturers are required to produce documents that demonstrate the quality and reliability of their products, and reputable manufacturers will be happy to provide them. We have found that many low-cost manufacturers are using unbranded, un-manufactured power products or counterfeit power products, which poses many problems for the final medical electronics OEM. If the manufacturer can’t come up with the relevant certification documents, and they just change the power of the POS terminal and then sell it as a medical power supply, then such a product will only make the user lose more. Therefore, for the selection of a good medical power supply, GMP qualification can prove the production and quality control of its products accordingly, but is such a product a good product? No, we must also grasp the performance parameters and reliability of the product, that is, whether the product has passed some international general specifications. EN60950 is an international safety specification for general purpose power supplies. Medical power supplies also need to meet the minimum basic requirements of this specification. However, the international safety regulations for medical power supplies are more stringent IEC601-1 A2, and there are three versions by region: EN60601-1 in Europe, UL2601-1 in the US, and CSA22.2 No 601.1 in Canada. These specifications cover technical indicators for electric shock protection, fire protection and machinery, as well as creepage distances and clearances, as well as test indicators for high-voltage insulation. Medical power supplies must be designed with appropriate design techniques to ensure stable operation during input anomalies and to operate under certain environmental conditions such as oxygen and/or anesthetic gases. Fire protection is also an important issue in these applications. 3. Leakage current: Leakage current is the current that flows through the protective ground conductor to ground. In the absence of grounding, if a conductive path (such as a human body) is present, the current can flow from the surface of the conductive or non-conductive component to the ground. There is always an external current in the safety ground conductor. Generally, the upper limit of the leakage current of a medical power source is one tenth of that of a normal power source. All power supply leakage current specifications of the IEC601 standard are much stricter than non-medical power supplies. The technical indicators define several different and most critical leakage currents, such as ground leakage current (flowing into the ground along the grounding body) and leakage current from the casing (through the patient from the casing into the ground). The maximum leakage current of the three main types of equipment power supplies is defined differently in the IEC601 standard: Class B: Equipment that does not come into contact with the patient’s body, such as a laser therapy device. Class BF: Equipment to be in contact with the patient’s body, such as ultrasound, various monitors (including EGC equipment), and operating tables. CF: A device that is in contact with the patient’s heart, such as a cardiac puncture monitor. People often misunderstand that the leakage current indicators of these device types are different. In fact, the allowable leakage currents of these types of devices are the same. North American specifications require more stringent leakage current than the European EN60601-1. For example, Europe allows 0.5 mA, while the United States and Canada only allow 0.3 mA. Therefore, medical device designers need to pay attention to the region where their products will be sold. BF or CF devices (commonly known as "contact with the human body") also require additional insulation to insulate the patient from the ground, signal port, and power output. This is to protect the patient in the event of an unexpected malfunction of the device and to keep the leakage current on the patient within the limits specified by the standard. This insulation can also be achieved by other parts of the final equipment, such as plastic probes or sleeves with sufficient insulation properties. However, in applications where patient power is required, one of the methods of treatment is to power one or more isolated DC/DC converters using an IEC601-1 compliant AC/DC power supply, plus a second level of insulation protection. Therefore, the DC/DC converter must be carefully selected to ensure that the insulation requirements are met. Since medical devices are often connected directly to the patient and conductive paths are formed through skin or even subcutaneous connections, the leakage current must be as zero as possible, the insulation must be reliable, and there must be no sneak current. 4: Security and isolation: Safety and isolation are also a major difference between commercial power and medical power, which is related to the safety of the patient receiving the treatment and the medical staff who use the equipment. Although human skin is a good insulator, once a very small alternating current is applied to the heart, it can cause fibrillation and neuromuscular damage to the heart muscle. Therefore, the environmental equipment involved in the patient, any part of the part that may be in contact with the patient must be strictly limited to 40-70Hz. The level of protection required for medical device applications is related to the proximity of the device to the patient. There are three levels of safety for insulation and protection indicators for medical system power. First, all offline power supplies must meet the basic safety requirements of the EN60950 standard. In addition, the medical power supply to be close to the patient must also comply with the IEC601-1 standard. In addition to meeting the above two requirements, the device that contacts the patient needs an additional isolation barrier to protect. Also, when the utility power is interrupted, the standby generator of the hospital will take a few seconds or a few minutes to supply power. Therefore, many medical power sources and devices that use such power supplies are powered by UPS system relays. Thus, the input waveform of the power supply may change and is no longer an ideal sine wave. Therefore, it is necessary to connect a medical transformer to the front end of the power supply to further improve the security level. Therefore, equipment used directly on the patient must meet the highest insulation specifications for all of these parameters. 5. EMI-RFI radiation and protection Electromagnetic and electromagnetic radiation protection of equipment is also an important parameter for medical power supplies, including surge and transient current strength, electrostatic discharge (ESD) levels, and radio frequency interference (RFI) protection. For medical power supplies, these electrical specifications must be three times that of commercial products of the same class. Many medical applications involve RF therapy devices or non-invasive electronic surgical instruments, so the power supply must be immune to interference and unaffected. Qualified medical power supplies shall comply with the EN60601-1-2 standard that is compatible with many of the EMC-related technical requirements. Not only that, the medical power supply must also meet IEC61000-4-2 ((electrostatic protection capability, required to reach 3kV), IEC61000-4-3 (radio frequency radiation protection capability, required to reach 3V/m), IEC61000-4-4 EFT (voltage Transient withstand capability, required to reach 1kV), IEC61000-4- 5 (mains surge current capability, required to reach 1kV and 2kV), IEC61000-3-2 (mains line harmonic requirements), IEC61000-3-3 (power line Flicker requirements), and EN55011 (Class A product or B product radiation limit) requirements. For this reason, power supplies complying with IEC601-1 standards generally comply with EN55022/11A equipment specifications, rather than the more stringent Class B EMC specifications. These devices can also be designed to comply with Class B EMC specifications, but additional complex filtering and shielding measures must be taken to increase the size and cost of the device. The medical power modules of Guangzhou Jinshengyang are in terms of product size, cost and performance. Safety and other aspects have made a good balance. There are other requirements related to specific applications: if the system may be used on an ambulance, there will be a voltage shock. For this, the power supply should at least comply with the IEC 68-2-29 standard; some devices are portable devices. It may be used on helicopters and random vibrations may occur. For this, the power supply shall comply with MIL-STD-810E. Case: Some customers have used a low-cost "medical power supply", which has a power supply voltage of 5V and a current of 200mA. The unit price of a few hundred batches is $5. Devices that use this type of power supply sell for tens of thousands of dollars. The power supply, which is surprisingly low, seems to be very good. If it is too suspicious, it is true. After disassembling this power supply, it found that it had only one single-sided printed circuit board, and to save cost, the board did not have metalized through holes. The board is surface mounted and has a high component density. The component spacing does not meet the creepage distance requirements and design criteria specified by the medical power source and related safety management agencies. Leakage current reaches 900mA, far exceeding the specification limit. The creepage distance and clearance voltage specifications are also not up to the voltage used in the universal power supply. The spacing between the high voltage areas is only 0.5 mm, and solder resist is used to improve the resistance of the point medium. The pin spacing of the power MOSFET should have been increased to increase the creepage distance, but this power supply did not handle this, probably because of the manufacturing cost and doing so. The aluminum heat sink is inserted into the board through some claws and then soldered. Once the handling is not correct, the heat sink is prone to loosening. The MOSFET in the flyback circuit is a factory-free fullpak package with a silicone jacket and an insulating tape attached to the heat sink, which prevents the device from coming into contact with the heat sink, which may cause severe heat during use. The stability problem is that the heat sink is still cold when the MOSFET has overheated. This power supply meets commercial EMI-RFI requirements but does not meet medical power requirements. There are other problems with this type of power supply, such as the presence of solder joints throughout the power supply. When used, even if it is properly assembled, it may not be possible at what time. This kind of power supply, although sold as a medical power source, is not originally designed according to medical requirements. Except for input voltage and output voltage and current, there are no relevant documents and technical indicators. In addition to the surprisingly low price of this type of power supply, other performance requirements are far from the requirements of medical power supplies. Why do some people just want to reduce the cost of power to such a level and deliberately take so many risks? After all, the power supply is the main source of risks and dangers such as high temperatures, high voltages, noise, leakage currents, and fire. Therefore, when selecting and purchasing medical power supplies, the risks involved must be considered and must be purchased from a reputable manufacturer that provides documentation that meets relevant regulatory standards and complies with quality and reliability standards and requirements. Three: Typical applications for medical power: By understanding the various options for medical power, we will talk about several typical applications for medical power: 1. Application of ECG detection circuit: The following is a common type of ECG detection circuit, as shown in Figure 1. 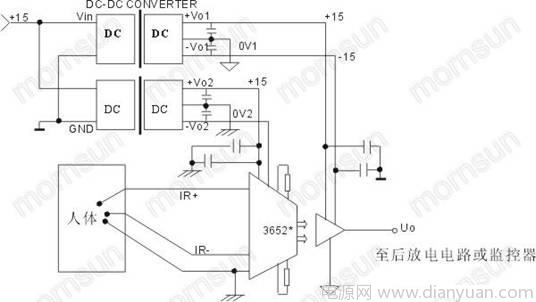
As shown in the figure, this circuit is a human body ECG detection circuit composed of ISO122 and INA115. The circuit can fully meet the requirements of medical device use, namely, low input impedance, low leakage current, high detection accuracy and human body safety. The ISO122 is isolated and transmitted to the post-amplifier circuit to realize the isolation and amplification of the human body signal and the output and the power supply. The isolated DC-DC module can effectively suppress the electromagnetic interference of the surrounding environment and eliminate the ground loop. 2. Patient ECG monitoring circuit The following is the patient ECG monitoring circuit, as shown in Figure 2 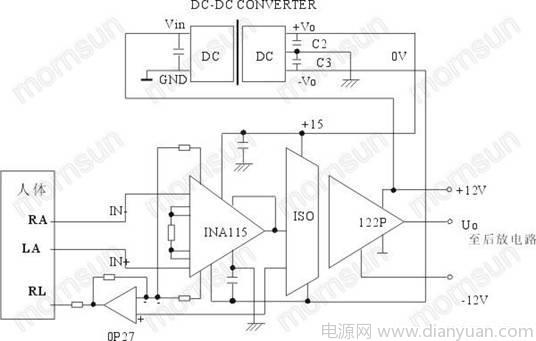
As shown in the figure, this circuit is an application of the 3652 in the patient ECG monitoring system. This circuit is a balanced input connection. The impedance of both the common mode and the differential mode input is very high, which can greatly reduce the frequent encounters in the monitoring equipment. The problem of common mode noise interference caused by the interference of the lead impedance interference; due to the use of the DC/DC converter G1515S-1W, the ground wire that the 3652 touches the patient is truly isolated from the input power line, in addition, 3652 Allows a continuous isolation voltage of 2000V between input and output, allowing isolation of non-periodic pulse voltages up to 5000V, thus protecting patient safety. The above two application circuits recommend Jinshengyang’s 6000VDC isolation series products (Fig. 3). The products fully comply with the specifications of medical power supply and have passed various medical certifications in the IEC601 standard. The isolation capacitor value is extremely small (≤10pF), the leakage current is small, safe and guaranteed. four. Conclusion: As far as the medical power supply modules on the market are mixed, the medical electronics industry is a special industry, and its power supply requirements are very high. To ensure the safety performance of the human body and equipment, it is particularly important to select a medical power supply module. The above mainly introduces the main performance requirements of medical power modules and some typical applications and precautions of medical power modules in the medical electronics industry. I hope this article can bring the corresponding medical electronic power to the medical electronic designers. help. |